Suitable for processing small places, and acute angled contour
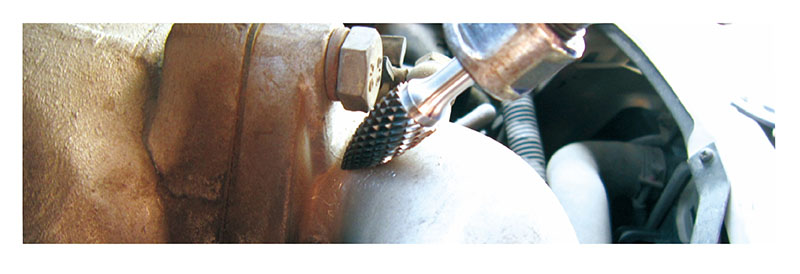
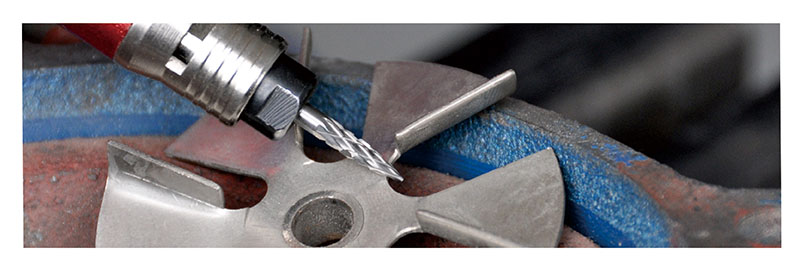
◆ Made by high quality tungsten carbide material. High wear resistance and long tool life.
◆ Grinded by high quality diamond grinding wheel. Sharp cutting edge and very fine finish.
◆ Manufactured by advanced CNC machine. High consistency and quality assurance.
◆ 100% testing on welding strength, assurance for users' safety.
◆ Well-designed cutter angle for optimum cutting efficiency and stability.
◆ Strong R&D capability enables special design and solutions according to customers' specific requirements.
1.Work with maximum RPM in the recommended cutting speed. Do not use speeds below 3,000 RPM except in special cases. Running below the optimum speed will encourages chipping and premature wear.
2.The larger head and shank diameter is recommended from the appropriate list for higher efficiency.
3.Adopt correct chuck to clamp cutter shank. Chucks and collets must be absolutely concentric to avoid chipping and premature wear.
4.Over two-thirds of length of shank must be clamped to ensure safety.
5.Extra long shank burrs shall be performed at lower speed. Turn on the power or air tools after the burrs touch the work piece for safety reasons. Do not move the cutter from the work piece when using, and turn off the power or air tools before any movements.
6.Avoid reciprocation in processing which may cause cutting edge breaking and premature wear. Follow the order from right to left.
7. Reduce RPM when processing on one location continuously or materials with low heat conductivity. Never let the shank and head become discolored blue due to overheat, which will result in lower welding strength.
8.When machining very sticky materials, the use of a suitable lubricant is recommended to prevent blocking in chip space.